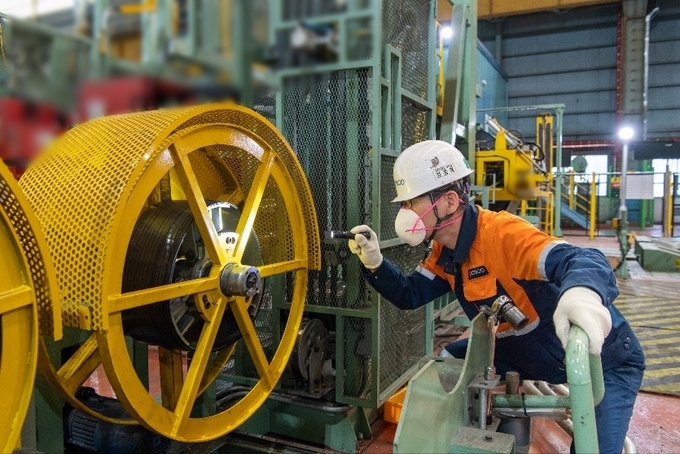
지이코노미 김정훈 기자 | 포스코 광양제철소(소장 고재윤)가 또 한 번 스마트한 현장 혁신을 이뤄냈다. 광양제철소 2열연공장은 최근 열연 코일의 스틸밴드 결속 공정을 자동화하는 장치를 자체 개발해 상용화에 성공했다. 이번 성과로 연간 약 3억 6,000만 원에 달하는 비용 절감은 물론, 작업자 안전성까지 크게 향상되며 명실상부한 ‘스마트 제철소’로의 진화를 가속하고 있다.
열연 코일은 마치 두루마리 휴지처럼 둥글게 말린 강판으로, 운송 및 보관 중 풀리지 않도록 스틸밴드로 단단히 묶는 작업이 필요하다. 지금까지는 이 공정이 대부분 수작업에 의존해 왔다. 작업자는 고열과 중량물에 가까이 접근해야 했고, 강철 밴드를 직접 감고 용접하는 과정에서 부상 위험도 컸다.
그러나 이번에 2열연공장이 도입한 자동화 장치는 이러한 위험요소를 원천적으로 차단했다. 열연 코일이 생산되면 센서와 로봇팔이 자동으로 위치를 인식하고, 스틸밴드를 감아 정확한 위치에 용접까지 마무리한다. 한 치의 오차도 없이 정교하게 이루어지는 작업 덕분에 품질의 균일성도 확보할 수 있게 됐다.
이 자동화 장치는 광양제철소 기술개발팀과 현장 작업자들의 협업으로 탄생했다. 기존 설비와의 호환성, 유지보수의 용이성, 안전기준 충족 등을 꼼꼼히 따져 수차례 시뮬레이션과 테스트를 거쳤고, 결국 현장 적용에 성공했다. 상용화 이후 약 6개월 만에 가시적인 성과가 나타났고, 연간 3억 원 이상이 절감되는 것으로 분석됐다. 이는 설비 유지비는 물론, 인건비, 사고로 인한 손실까지 포함한 수치다.
광양제철소 관계자는 “이번 자동화 시스템 도입은 단순히 비용을 줄이는 수준을 넘어, 작업자들의 안전을 지키고, 생산의 연속성과 품질까지 확보한 점에서 매우 의미 있는 변화”라며 “앞으로도 사람 중심의 스마트팩토리 구현에 힘쓸 것”이라고 밝혔다.
포스코는 이미 여러 공정에서 자동화와 디지털 기술을 적극 도입하고 있으며, 광양제철소 역시 '스마트 제철소'라는 미래 비전을 현실로 바꾸기 위해 각종 R&D와 현장 중심의 혁신을 지속하고 있다. 이번 2열연공장의 성공 사례는 향후 다른 공정에도 도입될 예정이며, 전사 차원의 자동화 전략에도 큰 힘을 실을 것으로 기대된다.